Trong Chiến lược phát triển công nghiệp (CN) dệt may Việt Nam đến năm 2015, định hướng đến 2020, một mục tiêu quan trọng là phát triển gắn với bảo vệ môi trường cùng xanh hóa trong sản xuất (SX). Vì thế, các biện pháp xanh hóa SX bằng việc tiết kiệm năng lượng (TKNL), xử lý nước thải, tái chế phế phẩm… đang được nhiều doanh nghiệp (DN) áp dụng.
Hiệu quả thấy rõ
Thực hiện mục tiêu trên, nhiều DN đã đẩy mạnh giải pháp quản lý và đổi mới công nghệ, thực hiện tốt trách nhiệm xã hội cũng như tiêu chuẩn SA 8000, bước đầu phát huy hiệu quả. Ông Dương Khuê – Tổng Giám đốc Tổng Công ty Dệt may Hà Nội (Hanosimex) cho biết, DN hoạt động SX sợi – dệt may nên vấn đề môi trường chủ yếu là khí thải, bụi và tiếng ồn khi kéo sợi. Để giải quyết vấn đề này, Hanosimex đã đầu tư nhiều hạng mục nhằm tiết kiệm nguyên, nhiên, vật liệu, NL cũng như tạo môi trường lao động trong sạch: Đầu tư hệ thống hút bụi tại các phân xưởng, nhà máy dệt; dùng mẩu vải thừa tại các dây chuyền may để SX đệm… Tại các lò cấp hơi sử dụng nước mềm nên giảm được 3 – 5% ô nhiễm không khí và tăng hiệu suất lò hơi. Đặc biệt mới đây, Hanosimex đầu tư gần 500 triệu đồng lắp các biến tần cho quạt thông gió của hệ thống điều hòa không khí, sử dụng toàn bộ bóng đèn TKNL T8 trong nhà máy, lò hơi chuyển đổi từ nhiên liệu đốt than sang đốt trấu hoặc mùn cưa ép. Nhờ đó, mỗi năm, Hanosimex tiết kiệm trên 4 triệu kWh điện, giảm phát thải khí CO2 tương đương 4.000 tấn/năm…
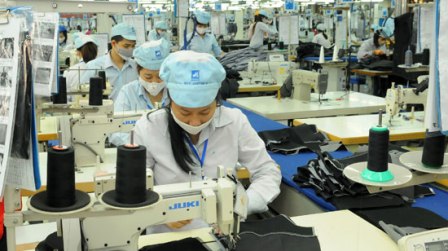
Dây chuyền sản xuất hàng xuất khẩu tại Công ty CP May 10
Đối với Công ty CP Dệt CN Hà Nội, việc cắt giảm chi phí SX và nâng cao khả năng cạnh tranh thông qua đầu tư sử dụng TKNL là một lựa chọn đúng đắn. Hiện, Công ty có Xí nghiệp vải mành và Xí nghiệp vải không dệt, sử dụng NL điện và nhiệt để phục vụ SX. Năm 2012, chi phí tiền điện gần 8 tỷ đồng, chi phí than cho lò hơi gần 5 tỷ đồng. Nhận thấy lượng tiêu thụ NL rất lớn, chiếm đến 5% giá thành SX, ban lãnh đạo DN bắt đầu chú trọng tiết kiệm và sử dụng NL hiệu quả. Được tư vấn của các chuyên gia kiểm toán từ Công ty Systech Eco, đơn vị đã đẩy mạnh các giải pháp khai thác tối đa tiềm năng TKNL, như: Bố trí lại lao động, làm việc theo ca, tránh sử dụng nhiều điện giờ cao điểm… Việc bảo dưỡng thiết bị được quản lý theo tiêu chuẩn ISO, xây dựng cơ chế quản lý NL dựa trên định mức tiêu thụ. Từ đó, tổng giá trị tiết kiệm ước đạt hơn 33 triệu đồng/năm. Sau 2 tháng chạy thử nghiệm các giải pháp, từ hiệu quả đã đạt được, ban lãnh đạo Công ty cho biết, sẽ đầu tư lắp biến tần cho 3 động cơ quạt cấp nhiệt còn lại, lắp biến tần cho các bơm có công suất lớn, thay dần đèn T8 thành T5 để đảm bảo tối ưu hóa hiệu suất hoạt động của thiết bị và hiệu quả sử dụng NL.
Tăng đầu tư cho môi trường
Theo ông Đặng Vũ Hùng – Phó Tổng Giám đốc Tập đoàn Dệt may Việt Nam (Vinatex), trước đây, “giấy thông hành” đối với nhà SX dệt may thường chỉ là tiêu chuẩn về trách nhiệm xã hội, nhưng sắp tới, nhiều nhà NK sẽ đề ra thêm các tiêu chuẩn về môi trường bền vững. Trong đó, phổ biến nhất là tiêu chuẩn SX xanh, xử lý nước thải, giải pháp tái chế phụ phẩm phát sinh trong SX. Tuy nhiên, một rào cản lớn của ngành dệt may là DN thường có quy mô vừa và nhỏ, công nghệ lạc hậu… dẫn đến chi phí SX cao, lợi nhuận thu về chưa nhiều. Theo tính toán, để tạo một tấn hơi nước cho dây chuyền SX, mỗi ngày, công nhân phải đốt ít nhất 700 lít dầu. Vì thế, việc tìm ra những giải pháp tiết kiệm chi phí SX nói chung và TKNL nói riêng cần được đặt lên thành mối quan tâm hàng đầu của các lãnh đạo DN nhằm tăng lợi thế cạnh tranh cho sản phẩm trên thị trường.
Về phía Vinatex, để đảm bảo yếu tố phát triển bền vững, Tập đoàn đã xây dựng kế hoạch tăng cường kinh phí đầu tư hoàn thiện các tiêu chuẩn về môi trường ở các lĩnh vực như hoàn chỉnh hệ thống xử lý nước thải, hệ thống cách nhiệt, TKNL, tạo môi trường làm việc thông thoáng…